Company Name | Contact Info | Location | ||||||||||||
---|---|---|---|---|---|---|---|---|---|---|---|---|---|---|
WERTE KESİM TEKNOLOJİLERİ SAN.TİC. LTD. ŞTİ.
Yakacık Çarşı Mah. Çam Sok. 43/B / Kartal / İSTANBUL / TÜRKİYE
|
Contact Info: +90 216 706 7060
|
Hall: 7
Stand: 706
|
||||||||||||
Product Groups | ||||||||||||||
|
- Company Info
- Products
- Represented Companies
- Company Brands
In addition to being Turkey s first micro lubrication system manufacturer, Werte is an innovative technology company providing comprehensive solutions for pipe manufacturing plants. Together with our Italian representatives, we bring the most advanced technologies in the industry to our customers. Our solutions include Tube Slitting Machines Ensures precise slitting of coil sheets. Tube Entry Lines Optimizes coil feeding, alignment, and welding processes. Tube Mills Provides high precision in the production of carbon steel, stainless steel, and aluminum tubes. Tube Cutting Machines Equipped with cold saw and flying shear cutting technologies. Tube Cutting Saws Enables high-speed cutting for different tube diameters and wall thicknesses. Tube Packaging Machines Ensures the orderly and secure packaging of tubes. Tube Lubrication Machines Optimizes lubrication during production, enhancing quality. Tube Welding Machines Developed for high-durability welding processes. At Werte, we are making a difference in the tube manufacturing industry by providing high-efficiency, high-quality, and precision-focused solutions. Together with our Italian representatives, we continue to deliver the most advanced technology and services to our customers.
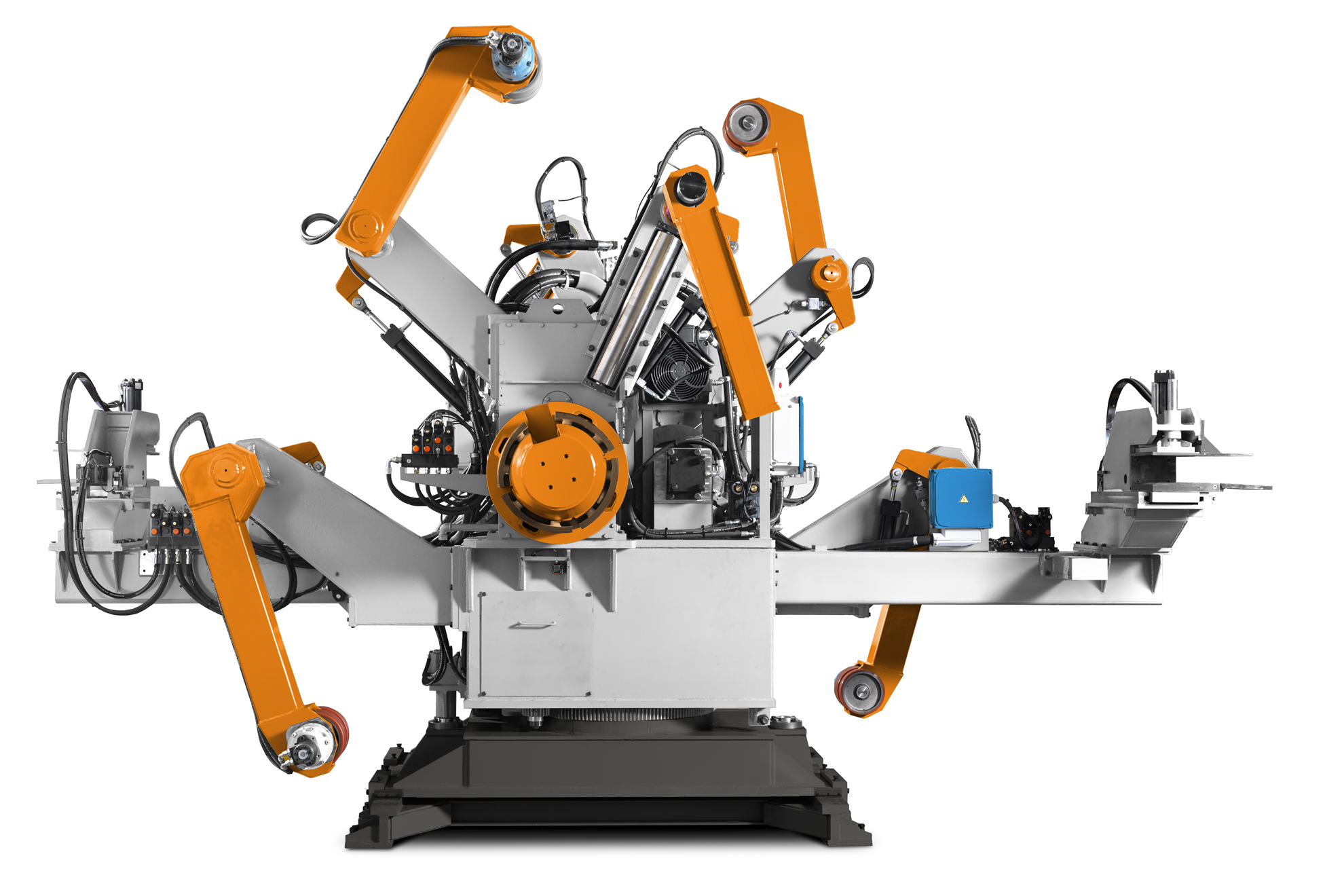
MTM ENTRY LINES cover the complete range of solutions for coil handling, from coil loading - preparation and unloading, strip joint and traceability, to accumulation and strip feeding into the forming section. MTM ENTRY LINES fit out the highest level of automation able to guarantee the increasing of plant productivity and eliminating machine downtime. In accordance with the requested level of automation, the MTM ENTRY LINES are equipped with coil handling conveyor, coil turnstile, coil lifting car, coil upender, double or single decoiler with clamping arms, feeding pinch -roll, strip flattener, strip shear & welder, welding joint annealing system and milling, strip accumulator
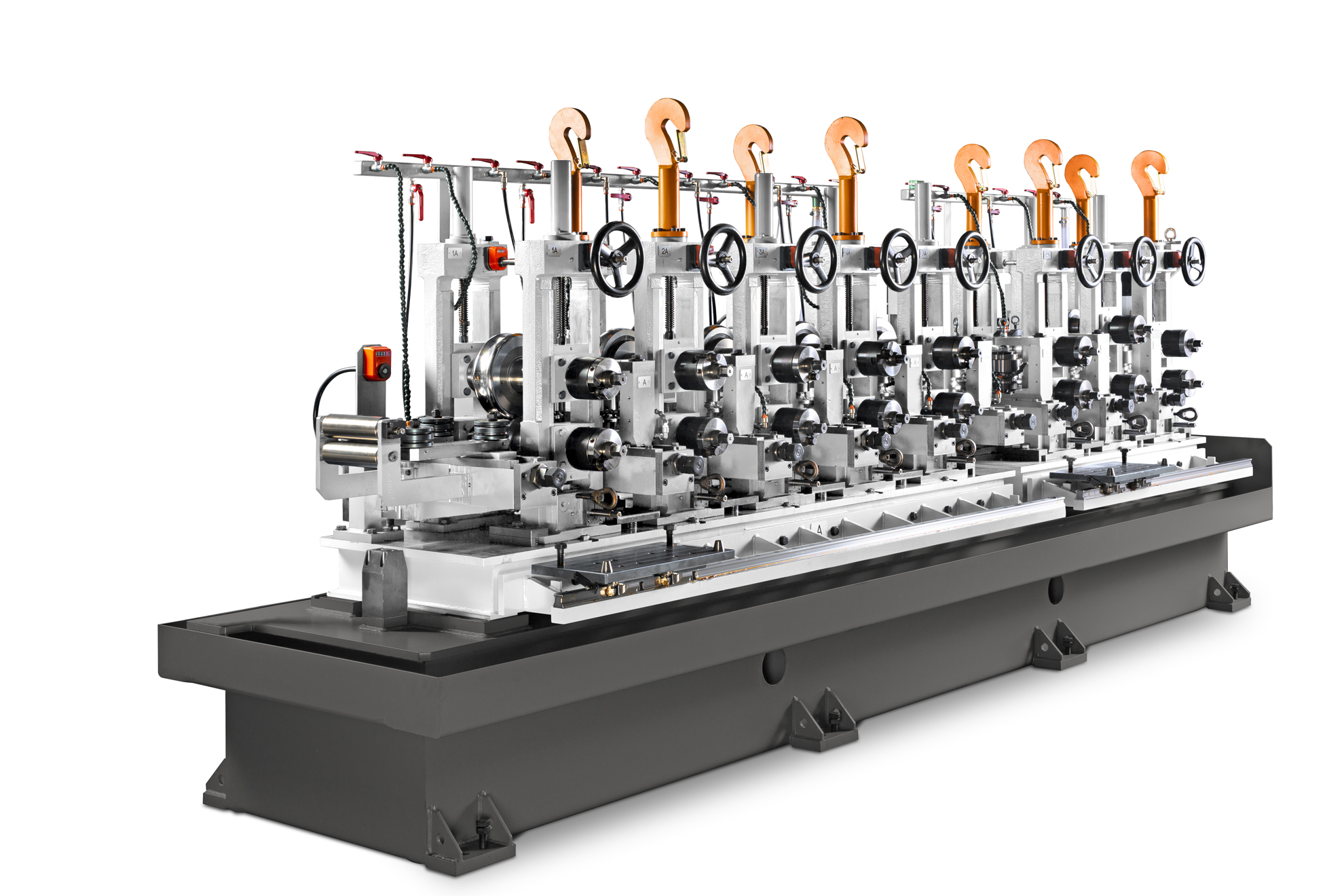
MTM TUBE MILLS are designed to cover a wide range of solutions for the production of carbon steel, stainless steel and aluminum ERW tubes from 6,0 mm to 254,0 mm Outer Diameter and from 0,2 mm to 12 mm Wall Thickness. MTM TUBE MILLS are recognized for their high level of automation and precision. They are equipped with advanced in -line control systems that guarantee the constant control of the process parameters as well as the quality and reliability of the production. The QC Series offers the tooling quick - change systems, thanks to whom it is possible to perform fast production changes, minimizing the tube mill downtime and guaranteeing high levels of productivity.
Developed since over 45 years ( 5 decades ) , the MTM CUTOFF MACHINES are designed to perform different type of cutting processes like the cold saw or friction saw, the double - blade orbital or alternate cutting and the flying shear cut. MTM CUTOFF MACHINES are well - known all around the world for their high precision and performance levels in terms of quality and reliability standards. The EVO 2 -CUT software has been developed by Officine MTM in order to allow an easy and intuitive control and set up of the machine. With the WIZARD module, it is possible to set the machine following an icon based wizard, according to the type of pipe to be cut and the blade to be used.
GTC s classic plant for the packaging of round, square and rectangular tubes. The ejection of the package is lateral, and the plant can be implemented with systems for draining and weighing, automatic or manual strapping, blowing, warehousing, etc. The peculiarity of this variant, which is offered on the Asian market, where the weight/dimension relation is decisive, is that, compared to a frontal packaging plant, it gives the possibility to create bundles with notable weight and dimensions. Starting from standard tube size ranges (1 -5 ), the bundles can get up to 7 Tons of weight. All the regulations can be manual or automatic.
GTC s plant collects the tubes by means of a run-out conveyor that transfers them to the packagin area. Each tube is aligned with the others and moved to the bundle formation area, where a specific system rotates it alternately of 180° to adapt it to the one below. Successively the row is deposited on the structure where the bundle, which is then set on the evacuation cart, is formed. The cart collects the bundle and transfers it outside the packing machine, where a strapping machine completes the process. The plant, then, transfers the bundle to the weighing station followed by the warehousing area, freeing the cart and returning it underneath the packing machine, now ready to accept a new bundle.
GTC s tube end-facing and chamfering machine is suitable to automatically work the tube head/end, outer and inner parts by means of marker tools. All the machining operations comply with the API standards. The feeding of the chamfering heads can be performed by means of a walking-beam system or motorized transport chains. Through simple adjustments, the center of tube is kept aligned with the tools processing axis, in order to reach a perfect head beveling. The machine s extreme flexibility enables a seamless integration with the tube production line, and it can be placed upstream of a washing station, a packaging plant or an hydraulic test station. According to customer s needs and tube line production speed, the system can be equipped with either single or double head system and with or without quick change of the chamfering and end-facing tools.
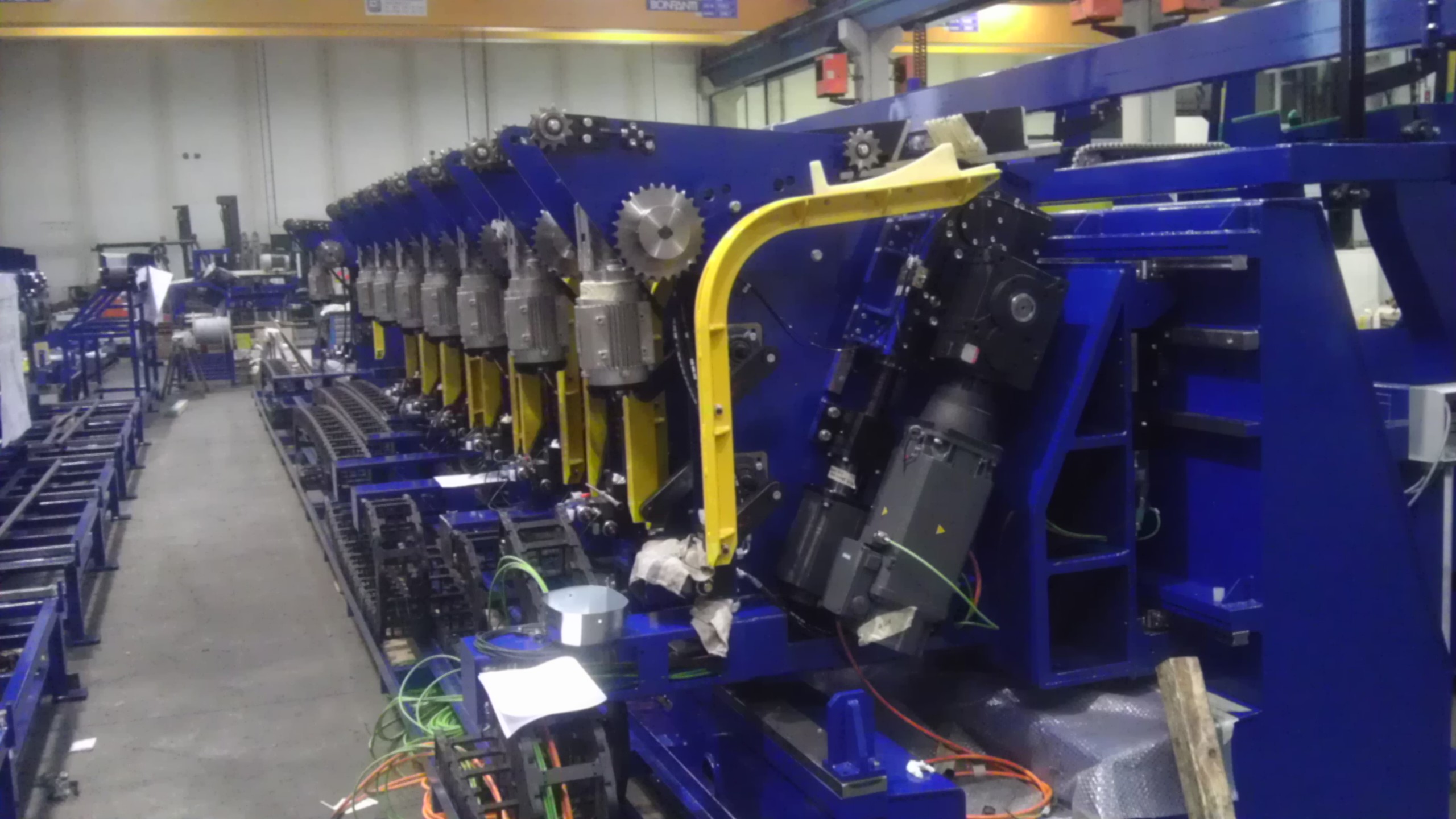
GTC s cross-cut saws are designed to perform simultaneous cuts through independent heads that can be positioned according to the requested length of the cut. Blades for particularly tough materials can be installed on these machines, and the velocity, both of the blades and of the advancement of the tubes, can be adjusted. The number of cutting heads installed can be adapted to specific needs.
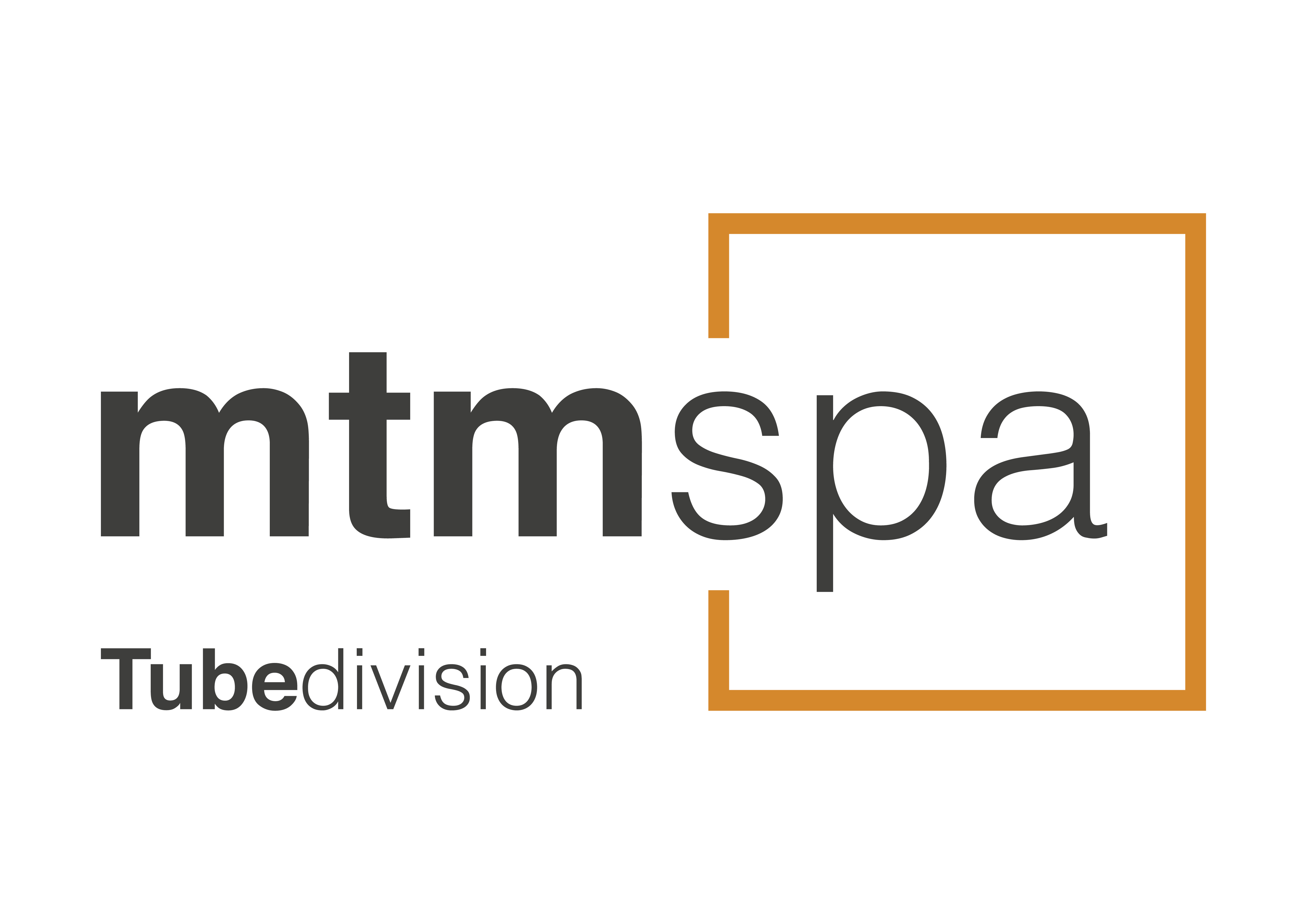
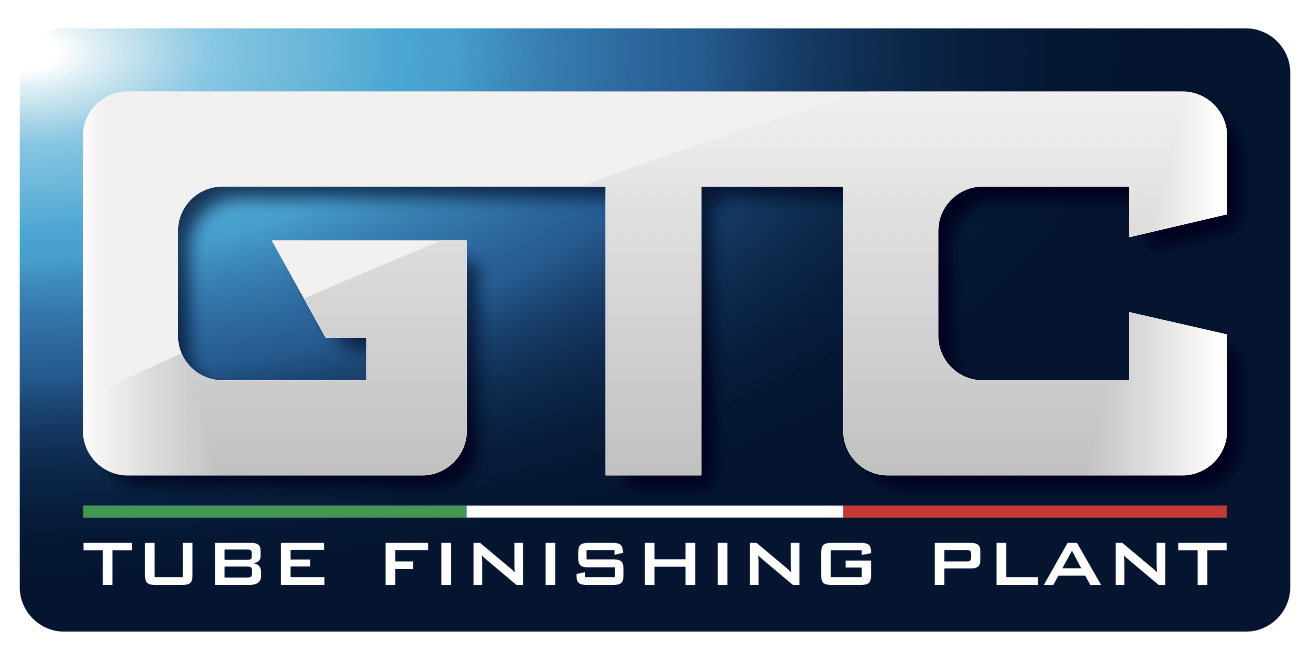
The company has no registered brand information.